Electric forklift manufacturers will be quick to tell you that electric forklifts are better for the environment, compared to conventionally powered diesel and gas forklifts. We at Forkify decided to do a bit of digging into the numbers to see if their claims stack up (no pun intended) and if different battery technologies have an impact.
How electric forklifts are different
In recent years, electric forklift trucks have gained popularity in the industry owing to stricter regulations on pollution and noise levels. Electric forklifts have also improved significantly, and are now considered just as reliable and durable as their fossil-fuel counterparts. One advantage of electric forklifts is their compact size, which allows for enhanced mobility and the ability to stack items in confined spaces. This makes them a great option for organisations looking to maximise their warehouse space.
One of the main benefits of electric forklifts is their lack of emissions, as they do not release any harmful pollutants and are more energy-efficient than other types of forklifts. Choosing electric forklifts shows that your organisation is environmentally conscious, which is increasingly important as companies seek to demonstrate their green credentials to the world. Without any internal combustion engines, electric forklifts are also quieter, have lower vibration levels, and are easier to maintain. They may also have a lower overall ownership cost, depending on several factors such as upfront cost, fuel/electricity cost, and reduced maintenance requirements.
Increasing popularity
Electric forklift sales are growing steadily, with the global market set to reach 75% by 2030.
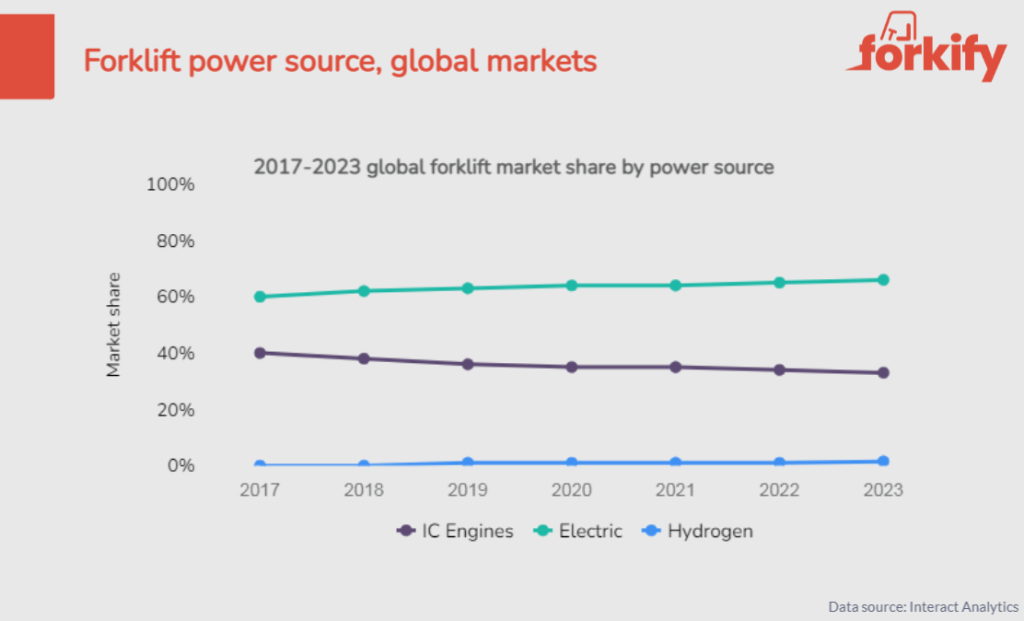
A graph showing the global market share of forklifts by power source
As the graph demonstrates, hydrogen forklifts are also gaining some popularity. Toyota is the main manufacturer currently investing in Hydrogen, but we may see more manufacturers taking up Hydrogen in the future.
We can also see that as the global market share of electric forklifts increases, demand for internal combustion-powered forklifts steadily decreases. Although the market saw a small contraction in 2022/23 owing to supply chain issues (primarily caused by COVID-19), it is expected to grow by 35-40% from 2024 until 2030.
Analysing the numbers
Running emissions
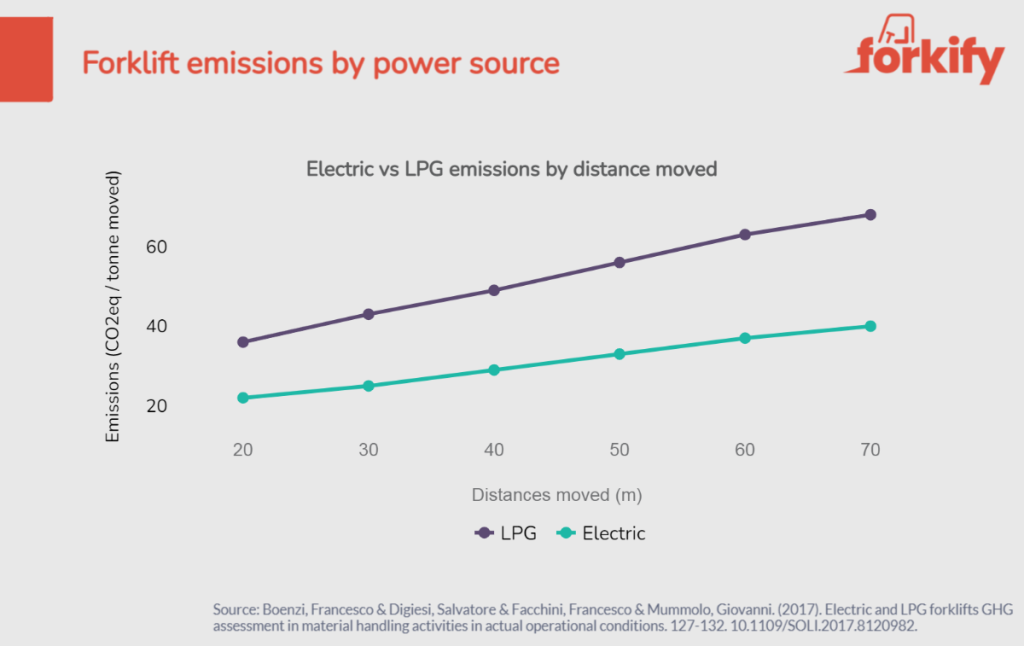
A graph comparing forklift emissions between LPG and electric power sources
The graph shows that electric forklifts have consistently lower CO2 emissions than LPG, with the gap widening as the forklift moves greater distances. The study takes into account several factors, such as the emissions associated with recycling/reconditioning the batteries on electric forklifts, in order to compare the two power sources. The emissions caused by charging electric forklifts are somewhat more difficult to establish, as this will vary depending on how the electricity is produced in different areas.
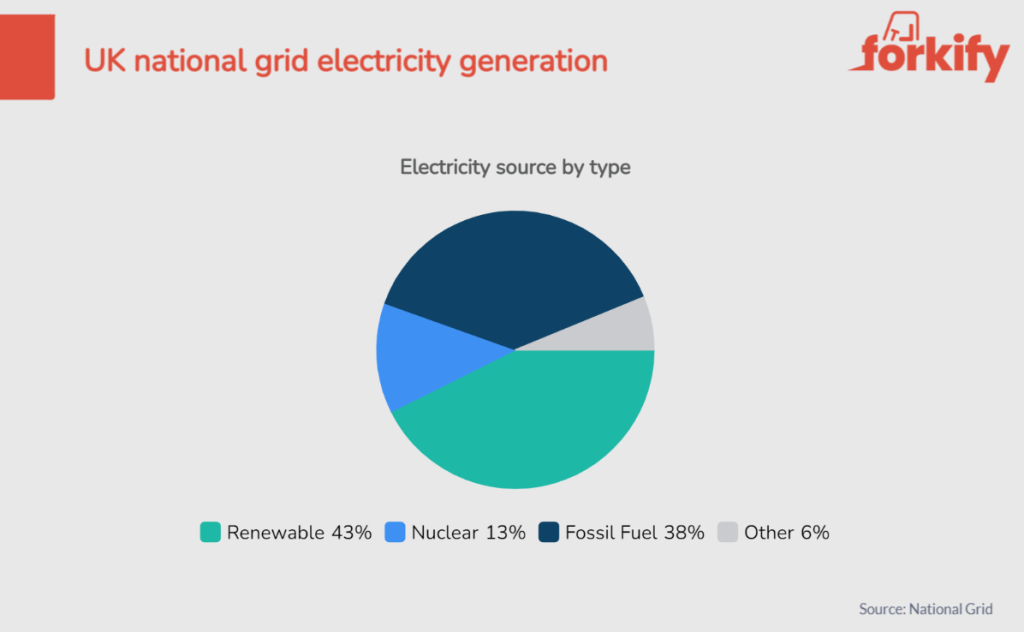
Pie chart showing UK electricity sources, November 2022
The chart above shows that renewable and nuclear energy combined provided more than half of the UK’s electricity requirements. Similar figures are accurate for many other European countries, with renewables making up a large percentage of the power mix. This goes some way to reducing the environmental impact of electric forklifts, and as countries continue to expand their renewable electricity capacity, the net electric forklift emissions will also decline. It’s worth noting that many countries use considerably more fossil fuels to produce electricity, so where the forklift is being charged will affect the environmental impact considerably.
It’s worth noting that as of 2024, renewable energy sources have not significantly changed as a proportion of the UK’s energy mix. Renewables have also been variable across the world, with Germany, for example, relying more on coal for power production from 2023 until March 2024. This has hindered the potential of electric forklifts to be truly green, although the situation is expected to improve by 2025 and beyond.
Production emissions
The production of diesel/LPG engines and batteries for electric forklifts involves several steps, including mining and processing raw materials, manufacturing various engine components, and assembling the finished product. It is important to note that these processes can contribute to CO2 emissions in multiple ways, including through the direct use of fossil fuels and through the indirect production and transportation of materials and finished products.
It’s worth bearing in mind that during the manufacturing process, a forklift typically produces a relatively small amount of CO2 compared to the total CO2 emissions it will generate over its lifetime. The majority of a forklift’s CO2 emissions typically come from the fuel/electricity used to operate it, rather than the energy used to manufacture it. There is a lack of data surrounding the emissions created by producing diesel, LPG and electric forklifts. Electric cars are considered, on average, to break even with IC engine emissions after 15,000 miles or so in the UK, although this is a generalisation that assumes many factors. An electric forklift that is used 2,000 hours per year will likely be breaking even on emissions, compared to IC engines, within 12-18 months.
Mining material for batteries
One major problem with producing batteries for electric forklifts is localised pollution, contamination and destruction of the environment. The physical extraction of lithium, for example, is a resource-intensive process that requires a large amount of water; about 500,000 gallons per metric tonne of lithium. The mining of lithium from salt brines in South America has raised concerns about the contamination of local water basins. In Chile, one of the driest places on earth, lithium mining consumes 65% of the region’s water, leading to the salinisation of freshwater sources used by local communities and farmers. Salinisation happens when the water in the soil evaporates, resulting in the accumulation of salt on the surface. This can be harmful to native plants and render the land unfit for use.
Lithium-ion vs lead-acid
The graph below shows that the UK market share of forklifts is heavily skewed to lead-acid batteries, which may increase the environmental impact of electric forklifts. As forklifts use lithium-ion batteries in greater numbers, the environmental impact will likely be lessened, especially when combined with proper lithium-ion recycling.
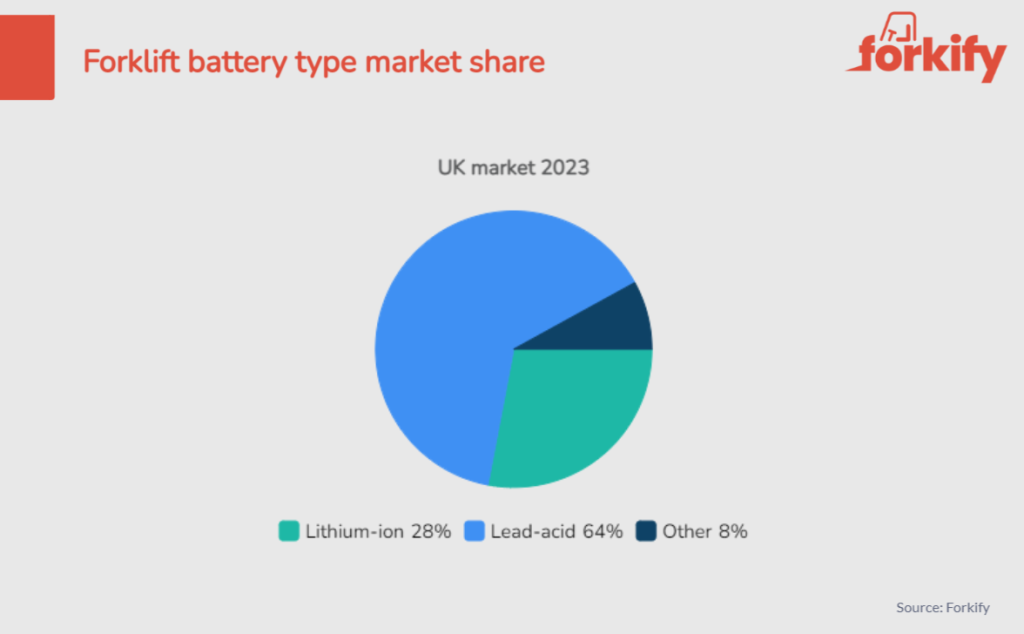
A pie chart showing the market share of forklift battery types
The production of lead-acid batteries requires a significantly larger amount of raw material, which results in a large impact on the environment during the mining process. The lead processing industry is also energy-intensive, contributing to pollution. Although lead is toxic to humans, the manufacturing and packaging processes for lead-acid batteries minimise the risk of harm to people.
Lithium-ion batteries also have environmental impacts owing to the mining of materials such as lithium carbonate, copper, aluminium, and iron ore. While the mining of lithium is resource-intensive, the mass of lithium in the battery cell is relatively small compared to the other materials. As a result, the environmental impacts of aluminium and copper mining are more significant. The lithium-ion recycling industry is still in its early stages, but the materials in these batteries have demonstrated a high potential for recovery and recyclability. It is anticipated that recycling rates for lithium-ion batteries will eventually approach those of lead-acid batteries. As it stands, in most countries the level of lithium-ion recycling is considerably lower than that of lead-acid recycling, which is an important consideration when analysing the impact of an electric forklift in operation today.
Another factor to consider is that lithium-ion batteries last considerably longer than lead-acid batteries. A typical lithium-ion forklift battery can provide 3,500 charge cycles before needing to be replaced, compared to only 500 on a typical lead-acid battery. This is an important consideration, as replacing lead-acid batteries more frequently will worsen the environmental impact.
The graph below compares CO2 emissions producing lead-acid and lithium-ion batteries. Compared to the factors already mentioned, these figures are not pertinent in most use cases, but should still be considered.
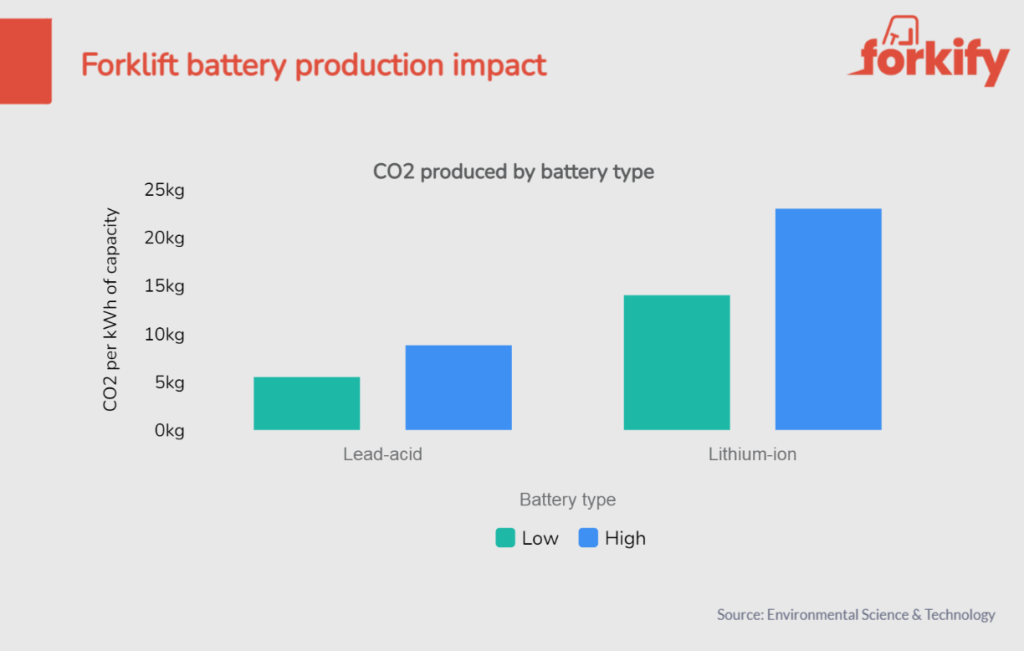
A graph showing the CO2 emissions per kWh of capacity produced, for lead-acid and lithium-ion batteries
The CO2 emitted will vary considerably depending on where the batteries are produced. The low and high values in the graph above correspond to the regional differences in power generation. China, the world’s leading producer of lithium-ion batteries, mainly relies on fossil fuels for power generation. The high values in the graph become applicable in that instance, compared to other countries which use more renewable energy.
Conclusion
Electric forklifts are becoming increasingly popular due to their environmental benefits and improved technology. They emit fewer pollutants, are more energy-efficient than their fossil fuel counterparts, and may also have a lower overall ownership cost. Electric forklifts are also quieter, have lower vibration levels, and are easier to maintain. However, it is important to consider the environmental impact of producing and charging electric forklifts, which can vary depending on the electricity sources used and the materials and processes involved in production. Overall, electric forklifts offer a more sustainable and eco-friendly option for material handling in various industries.